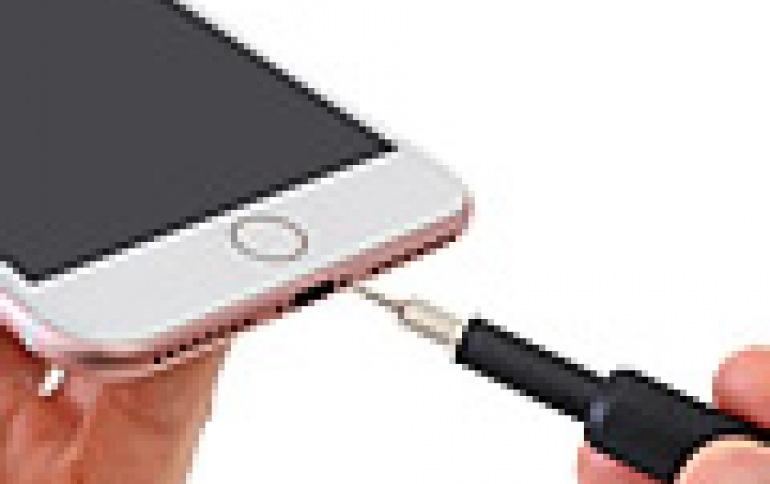
Apple Could Not Move iPhone Production To The U.S.
The recent election of U.S. President-elect Donald Trump and his criticism on overseas manufacturing are not enough to force Apple bring the iPhone production to the U.S., as costs would be very high, unless very high tariffs were imposed to Chinese imports.
Japanese newspaper Nikkei reports that Apple asked its key manufacturing partners in June to study the possibility of relocating iPhone production from Asia to the United States. Apple's decision was likely driven in part by U.S. President-elect Donald Trump?s threat of imposing tariffs on Chinese imports and his criticism of the tech behemoth?s use of overseas manufacturing.
But Apple has been relying entirely on contract manufacturers such as Foxconn and Pegatron to assemble its smartphones. These manufacturers, who largely operate out of China, help Apple keep costs low by leveraging Asia?s consumer electronics supply chain, which comprises major semiconductor fabs and component manufacturers that produce components ranging from displays to microprocessors to batteries. The region also has a relatively cheap labor pool.
It could prove very time-consuming and inefficient to shift production to the U.S., given the costs of uprooting and relocating manufacturing facilities. Moreover, staffing these facilities at scale could prove a challenge.
IHS estimates that it costs Apple roughly $225 to manufacture an iPhone 7 in Asia, with assembly costs standing at just about $5, or about 2% of the total cost. However, by some estimates, the cost of manufacturing an iPhone in the U.S. could be $30 to $40 higher, given the higher expenses associated with shipping components from various countries to the U.S. Costs could rise by an estimated $80 to $90 if the various iPhone components were to be made in the United States as well.
Apple currently assembles its Mac Pro desktop computer in the United States, but the product sells in small volumes and at very high price points ($3,000 and upwards) that justify the higher costs of manufacturing.
But Apple has been relying entirely on contract manufacturers such as Foxconn and Pegatron to assemble its smartphones. These manufacturers, who largely operate out of China, help Apple keep costs low by leveraging Asia?s consumer electronics supply chain, which comprises major semiconductor fabs and component manufacturers that produce components ranging from displays to microprocessors to batteries. The region also has a relatively cheap labor pool.
It could prove very time-consuming and inefficient to shift production to the U.S., given the costs of uprooting and relocating manufacturing facilities. Moreover, staffing these facilities at scale could prove a challenge.
IHS estimates that it costs Apple roughly $225 to manufacture an iPhone 7 in Asia, with assembly costs standing at just about $5, or about 2% of the total cost. However, by some estimates, the cost of manufacturing an iPhone in the U.S. could be $30 to $40 higher, given the higher expenses associated with shipping components from various countries to the U.S. Costs could rise by an estimated $80 to $90 if the various iPhone components were to be made in the United States as well.
Apple currently assembles its Mac Pro desktop computer in the United States, but the product sells in small volumes and at very high price points ($3,000 and upwards) that justify the higher costs of manufacturing.