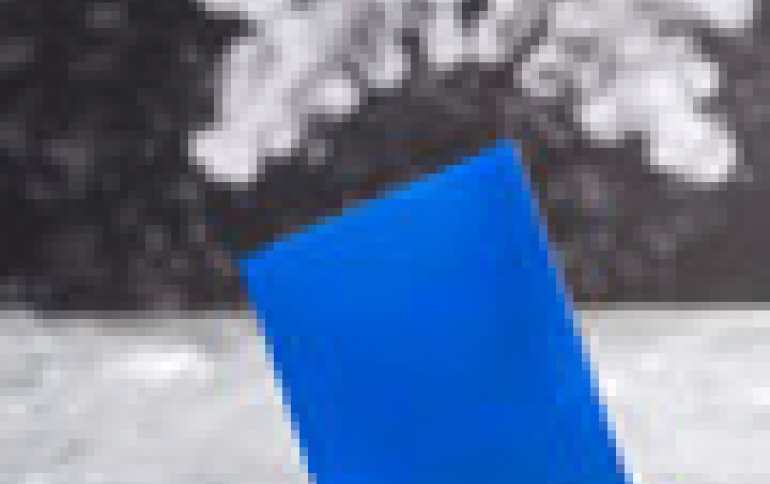
IBM Uses Self-assembling Material in Chip Advance
IBM has developed a way to make microchips run up to one-third faster or use 15 percent less power by using an exotic material that "self-assembles" in a similar way to a seashell or snowflake.
The company said the new process allows the wiring on a chip to be insulated with vacuum, replacing the glass-like substances used for decades but which have become less effective as chips steadily shrink.
It is the latest achievement for IBM researchers, who have announced a number of advances in recent months allowing chips to get smaller despite challenges posed by physical laws at those tiny dimensions.
"This is one of the biggest breakthroughs I've seen in the last decade," said John Kelly, IBM's senior vice president of technology and intellectual property.
"The holy grail of insulators is to use vacuum ... and we've broken the code on how to do this," Kelly said.
The technique works by coating a silicon wafer with a layer of a special polymer that when baked, naturally forms trillions of uniformly tiny holes just 20 nanometers, or millionth of a millimeter, across.
The resulting pattern is used to create the copper wiring on top of a chip and the insulating gaps that let electricity flow smoothly. A similar process is seen in nature during the formation of snowflakes, tooth enamel and seashells, IBM said.
"The problem they needed to solve was how to create lots of deep little wells in the insulation area between the wires," said Nathan Brookwood, who runs Insight 64, an industry consultancy.
"Typically, whenever they tried, they ended up making a chip that was like Swiss cheese and had no mechanical integrity," Brookwood said.
Kelly said that while IBM plans to use the process in its chips in 2009, it has already made prototypes based on existing designs and it could employ the technique sooner.
IBM will also "selectively license" the technology to partners, Kelly said. IBM has research efforts with No. 2 computer processor maker AMD, Toshiba, and others.
It is the latest achievement for IBM researchers, who have announced a number of advances in recent months allowing chips to get smaller despite challenges posed by physical laws at those tiny dimensions.
"This is one of the biggest breakthroughs I've seen in the last decade," said John Kelly, IBM's senior vice president of technology and intellectual property.
"The holy grail of insulators is to use vacuum ... and we've broken the code on how to do this," Kelly said.
The technique works by coating a silicon wafer with a layer of a special polymer that when baked, naturally forms trillions of uniformly tiny holes just 20 nanometers, or millionth of a millimeter, across.
The resulting pattern is used to create the copper wiring on top of a chip and the insulating gaps that let electricity flow smoothly. A similar process is seen in nature during the formation of snowflakes, tooth enamel and seashells, IBM said.
"The problem they needed to solve was how to create lots of deep little wells in the insulation area between the wires," said Nathan Brookwood, who runs Insight 64, an industry consultancy.
"Typically, whenever they tried, they ended up making a chip that was like Swiss cheese and had no mechanical integrity," Brookwood said.
Kelly said that while IBM plans to use the process in its chips in 2009, it has already made prototypes based on existing designs and it could employ the technique sooner.
IBM will also "selectively license" the technology to partners, Kelly said. IBM has research efforts with No. 2 computer processor maker AMD, Toshiba, and others.