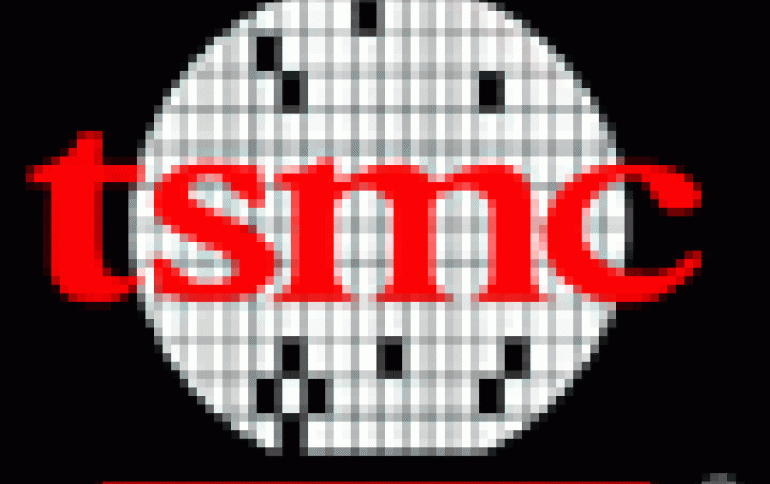
TSMC to Initiate 20nm Production Next Year
Taiwan Semiconductor Manufacturing Co. (TSMC) plans to start pilot production of its advanced 20nm process in the second half of 2012, as a first step to the company's transition to larger, 450mm-sized wafers.
Speaking at a VLSI forum in Taipei, TSMC's senior vice president in charge of research and development, S.Y. Chiang added that the company would also start using the 28nm process in volume production lines in the second half of this year. Pilot run of the 28nm process technology is scheduled to start in the second quarter of the year, he added.
Chiang noted that 28nm process can turn out more than twice as many chips as 40nm can on the same wafer. He added the company will complete pilot production of the process on 70 tapeouts throughout this year. Tapeout means the final step of IC design cycle at which the photomask of the IC is sent for manufacturing.
Chiang also estimated the Moore's Law, which concludes the number of components on an IC chip will double roughly every 18 months, will hit its limit in seven to eight years. This means that is will remain applicable in the semiconductor industry at least until 7nm process is introduced.
The transition to larger wafers (450mm) is expected to enable growth of the semiconductor industry and help maintain a reasonable cost structure for future integrated circuit manufacturing and applications.
Historically, manufacturing with larger wafers helps increase the ability to produce semiconductors at a lower cost. The total silicon surface area of a 450mm wafer and the number of printed die is more than twice that of a 300mm wafer. The bigger wafers help lower the production cost per chip. Additionally, through more efficient use of energy, water and other resources, bigger wafers can help diminish overall use of resources per chip. For example, the conversion from 200mm wafers to 300mm wafers helped reduce aggregate emissions per chip of air pollution, global warming gasses and water, and further reduction is expected with a transition to 450mm wafers.
TSMC is also expected to swift to solar energy and LED businesses in the upcoming years. The company believes that the thin-film technology the company is using to develop solar panels has potential both in cost efficiency and high photovoltaic conversion rate, compared to the currently available solar-energy equipment, which is mainly based on crystalline silicon.
Chiang noted that 28nm process can turn out more than twice as many chips as 40nm can on the same wafer. He added the company will complete pilot production of the process on 70 tapeouts throughout this year. Tapeout means the final step of IC design cycle at which the photomask of the IC is sent for manufacturing.
Chiang also estimated the Moore's Law, which concludes the number of components on an IC chip will double roughly every 18 months, will hit its limit in seven to eight years. This means that is will remain applicable in the semiconductor industry at least until 7nm process is introduced.
The transition to larger wafers (450mm) is expected to enable growth of the semiconductor industry and help maintain a reasonable cost structure for future integrated circuit manufacturing and applications.
Historically, manufacturing with larger wafers helps increase the ability to produce semiconductors at a lower cost. The total silicon surface area of a 450mm wafer and the number of printed die is more than twice that of a 300mm wafer. The bigger wafers help lower the production cost per chip. Additionally, through more efficient use of energy, water and other resources, bigger wafers can help diminish overall use of resources per chip. For example, the conversion from 200mm wafers to 300mm wafers helped reduce aggregate emissions per chip of air pollution, global warming gasses and water, and further reduction is expected with a transition to 450mm wafers.
TSMC is also expected to swift to solar energy and LED businesses in the upcoming years. The company believes that the thin-film technology the company is using to develop solar panels has potential both in cost efficiency and high photovoltaic conversion rate, compared to the currently available solar-energy equipment, which is mainly based on crystalline silicon.