
Sony Showcases BD-ROM Production Technologies
Sony organized a press event in Japan on September 1, 2006, where it presented its latest developments in the mastering process of BD-ROM media.
The company presented its production line, installed at the Shizuoka plant of Sony Music Manufacturing Inc. (SMM) in Yoshida, Shizuoka Prefecture, Japan.
Currently, Sony has established three-way framework with BD-ROM mastering plants in Japan, Anif Austria (Europe) and the U.S. (Terre Haute, Indiana). Sony's plans include the manufacture of 10 million pieces per month by the end of 2006. The breakdown will be 2.5 million pieces per month for each of the Shizuoka plant and Europe, and 5 million per month for the US.
Sony presented its Phase Transition Mastering (PTM) method. An inorganic material is used in the production of the stamper that is used to transfer the data pit patterns to the disc. Moreover, Sony chas chosen the spin coating method to form the 0.1 mm cover layer on the BD-ROM.
To create a stamper, Sony has developed a method to form pits by exposing a metal heat-sensitive inorganic material to blue-violet laser. The inorganic material changes phase from amorphous to crystal when exposed to the laser light through a heat chemical reaction. The material which is heated above a certain threshold level crystallizes. The crystallized region is then made soluble in developing fluid to form the pits. The resulting recorded marks are smaller than the laser spot.
According to Sony, the new thermal sensitive method is superior to the photosensitive method since the marks (pits) are more accurately formed. The company also claims that the number of production steps needed for CD/DVD mastering have been reduced from twelve to five and thus, the cost is also reduced. In addition, the consumption in chemicals is limited and the overall process maintenance costs are lower.
Sony has also succeeded in forming the 0.1 mm cover layer on the BD-ROM with an adequate uniformity using the spin coating method.
Previously, forming the cover layer on a BD-ROM disc included the following steps:
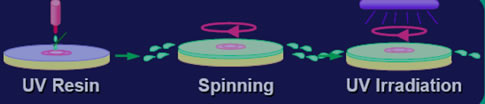
The peripheral portion of the disc generally tends to become thick when using spin coating. Sony has succeeded in producing a film with a uniform thickness by applying UV cure resin on the disc after filling the opening in the center of the disc. The variation in the thickness is within several microns, according to Sony.
Presently, the cycle times required to produce a disc of single - and dual-layer BD-ROMs at the Shizuoka plant are five and six seconds, respectively, whereas those required for DVD-ROMs is three seconds. The yield of BD-ROMs is 80% while that of DVD-ROMs is 95% or more. "The yields of CD-ROMs and DVD-ROMs at the beginning of the production were both rather low, namely about 15%. In comparison, the initial yield of BD-ROMs is significantly higher. It is possible to improve the yield by 10% through improvements in discharge conditions of spin coating and properties of the materials in the future," said Sony.
Currently, Sony has established three-way framework with BD-ROM mastering plants in Japan, Anif Austria (Europe) and the U.S. (Terre Haute, Indiana). Sony's plans include the manufacture of 10 million pieces per month by the end of 2006. The breakdown will be 2.5 million pieces per month for each of the Shizuoka plant and Europe, and 5 million per month for the US.
Sony presented its Phase Transition Mastering (PTM) method. An inorganic material is used in the production of the stamper that is used to transfer the data pit patterns to the disc. Moreover, Sony chas chosen the spin coating method to form the 0.1 mm cover layer on the BD-ROM.
To create a stamper, Sony has developed a method to form pits by exposing a metal heat-sensitive inorganic material to blue-violet laser. The inorganic material changes phase from amorphous to crystal when exposed to the laser light through a heat chemical reaction. The material which is heated above a certain threshold level crystallizes. The crystallized region is then made soluble in developing fluid to form the pits. The resulting recorded marks are smaller than the laser spot.
According to Sony, the new thermal sensitive method is superior to the photosensitive method since the marks (pits) are more accurately formed. The company also claims that the number of production steps needed for CD/DVD mastering have been reduced from twelve to five and thus, the cost is also reduced. In addition, the consumption in chemicals is limited and the overall process maintenance costs are lower.
Sony has also succeeded in forming the 0.1 mm cover layer on the BD-ROM with an adequate uniformity using the spin coating method.
Previously, forming the cover layer on a BD-ROM disc included the following steps:
- firstly, UV Resin was applied on the the disc
- next, the disc was covered with a polycarbonate sheet
- finally, the disc was exposed to UV irradiation
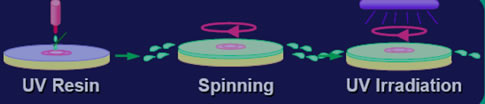
The peripheral portion of the disc generally tends to become thick when using spin coating. Sony has succeeded in producing a film with a uniform thickness by applying UV cure resin on the disc after filling the opening in the center of the disc. The variation in the thickness is within several microns, according to Sony.
Presently, the cycle times required to produce a disc of single - and dual-layer BD-ROMs at the Shizuoka plant are five and six seconds, respectively, whereas those required for DVD-ROMs is three seconds. The yield of BD-ROMs is 80% while that of DVD-ROMs is 95% or more. "The yields of CD-ROMs and DVD-ROMs at the beginning of the production were both rather low, namely about 15%. In comparison, the initial yield of BD-ROMs is significantly higher. It is possible to improve the yield by 10% through improvements in discharge conditions of spin coating and properties of the materials in the future," said Sony.