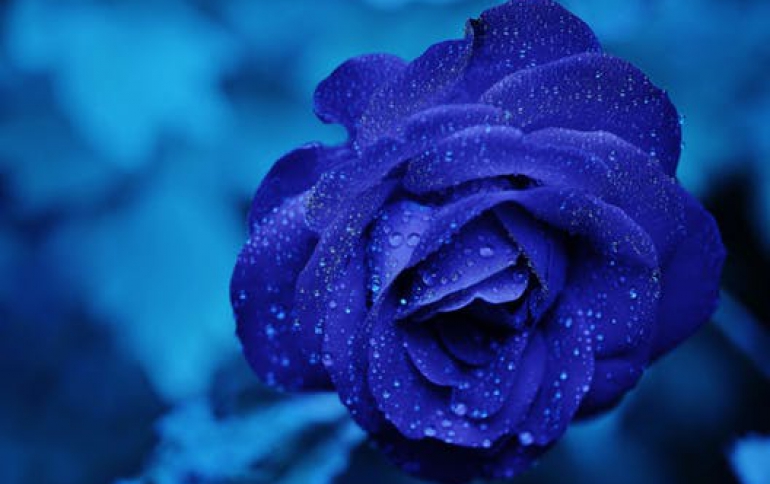
Toshiba Applies Spintronics Technology to Strain-gauge Sensor Element to Boost Sensitivity
Toshiba has developed an ultra-sensitive spintronic strain-gauge sensor element for micro-electro-mechanical-system (MEMS)sensors that is 2500 times as sensitive as conventional metal strain-gauges and over 100 times as sensitive as semiconductor strain-gauges.
The company has also developed the first spintronic MEMS microphone integrating a spintronic strain-gauge sensor element on the MEMS diaphragm, which has experimentally demonstrated accurate detection of ultrasonic sounds inaudible to the human ear.
Increasing adoption of the IoT is spurring demand for development of MEMS sensor technology for use in monitoring and fault diagnostics of industrial equipment, automotive equipment and infrastructure buildings. Many MEMS sensors comprise a movable part that deforms in response to external forces -- pressure and sound -- and a strain-gauge sensor element that converts the deformation into an electrical signal. The desire for highly accurate detection of small anomalous sounds in industrial and automotive equipment is driving efforts to improve the accuracy of MEMS sensors by increasing the sensitivity of strain-gauge sensor elements, with the goal of realizing strain sensitivity surpassing that of conventional semiconductor strain-gauges.
Toshiba has developed a new type of ultra-sensitive strain-gauge sensor element that employs spintronics technology -- a tchnology that utilizes both the charge and spin of electrons. MTJ elements (Magnetic tunnel junction elements consist of two magnetic layers with a thin insulating layer sandwiched between them), already used as hard disk heads and MRAM (magnetoresistive random access memory), can serve as the strain-gauge sensor element by employing the magnetostriction effect (the inverse magnetostriction effect), in which the magnetization of a magnetic layer changes depending on the strain. Toshiba says that strain sensitivity has been significantly increased by using amorphous iron-boron alloy materials, which have a large magnetostriction effect. The strain sensitivity of the new element is 2500 times that of a conventional metal strain-gauge and over 100 times that of semiconductor strain-gauges, allowing high-accuracy MEMS sensors using this element.
Toshiba has also developed the first spin-based MEMS microphone integrating a spintronic strain-gauge sensor element, and successfully demonstrated its operation, including accurate detection of ultrasonic sounds that exceed the frequency audible to the human ear. Conventional wide range microphones cannot detect these sounds, as the strain is insufficient to create electrical signals. Installing the Toshiba-developed spintronic strain-gauge sensor realizes both wide range sensitivity and high accuracy, which are normally trade-off, one or the other. This ability to capture operational sounds over a wide frequency range is promising for monitoring and fault diagnosis applications in a wide variety of equipment.
Toshiba will provide details on the technologies on June 19 at the Transducers 2017 international conference held in Taiwan.